Die casting has evolved into an integral manufacturing method in Malaysia which is a major contributor to the growth of Malaysia’s industry. This process involves the forming of molten metal in a mold using high pressure in order to produce intricate and precise parts, has transformed the way that industry produces parts that are used in many different uses. Because it can produce robust and high-quality components swiftly and easily it has been an increasingly popular method for industries such as electronics, automotive as well as aerospace. In Malaysia Die casting has been incorporated into the production process, helping local industry meet national and international requirements for premium metal parts. With the advancement of technology and advance, die casting is important to Malaysia’s efforts to remain ahead of the curve in the world of manufacturing.
One of the major advantages for die-casting in Malaysia is its capacity to make parts with incredible accuracy and precision. Die casting allows for the production of parts that have tight tolerances, intricate geometries as well as smooth finish and are vital in fields that place performance and high-quality essential. This is especially important for the automotive industry in which die-cast parts are utilized for engine blocks, transmission housings and structural components. In allowing companies to reach extremely high levels of detail as well as accuracy, die-casting is now an accepted technique for making parts that need to be in line with strict requirements. The accuracy offered by die casting does not just improve the quality of the finished item, but it also reduces the need for further process, which could decrease time spent and production cost.
Another major reason behind the rising use of the process in Malaysia is the versatility of materials that it provides. Die casting can be utilized to create a variety of different metals such as magnesium, aluminum, zinc and copper alloys with distinct properties appropriate for various applications. Die casting of aluminum for example, is extensively used in the automotive sector due to its durability and lightweight characteristics. Die casting made of zinc, in contrast is typically used for manufacturing smaller, complex parts, particularly for the electronic and consumer product sectors. Its flexibility enables manufacturers in Malaysia to adapt their manufacturing in accordance with the needs of their business, offering custom solutions that improve both the performance as well as cost.
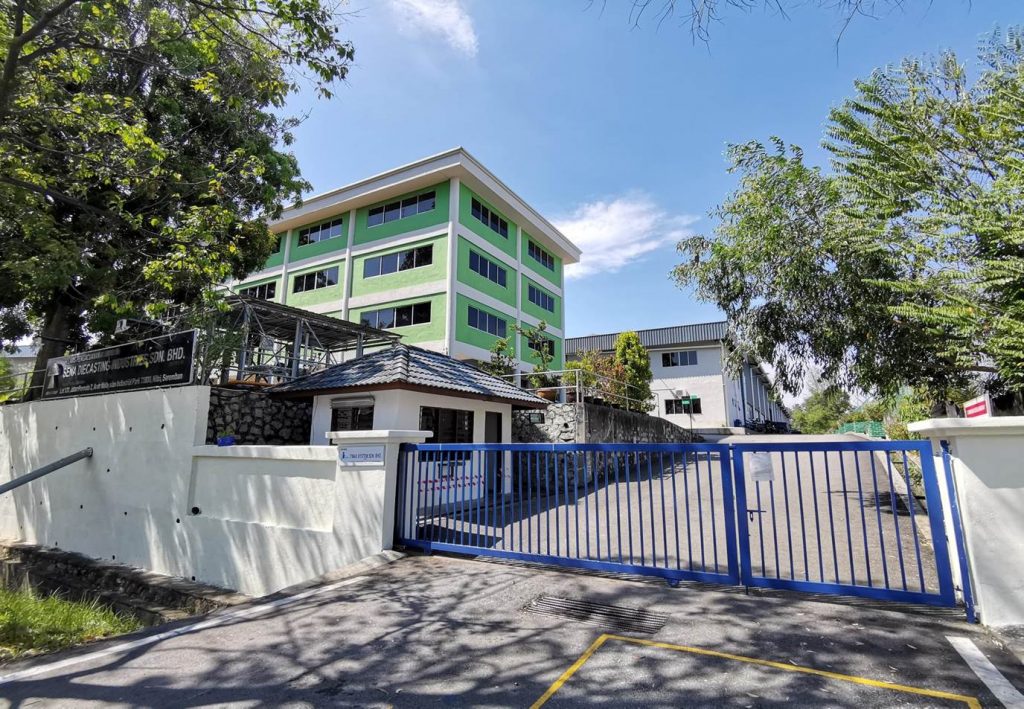
The efficiency and speed of die casting is a major draw for Malaysian manufacturing companies, especially for industries where large-scale production is crucial. Its ability to create massive quantities of components in a very short period of time make die casting the ideal choice to mass-production. After the mold has been created and used, it is able to be utilized over and over again to create thousands of the same components, which reduces lead times and increasing production. This can be particularly advantageous for industries like automotive manufacturing where components need to be produced in huge quantities in order to satisfy global demand for production. In addition, die casting needs less post-production processes that include the finishing process or machining. This makes it more cost-effective. In Malaysia’s industry of manufacturing grows in speed, the effectiveness and speed of die casting will ensure firms remain competitive both on the international and local size. For more information please visit here https://www.senadiecasting.com.my/
While it offers many benefits however, die casting in Malaysia is not without its challenges when it comes to the environment and sustainable management of resources. Die casting involves the use of metals that are molten, and produces emissions, waste as well as other byproducts that could cause environmental negative impact. In the end, the pressure is increasing on companies to use environmentally friendly practices as well as reduce the carbon footprint of their business operations. Numerous die casting firms are in Malaysia have responded to this need by adopting eco-friendly technologies, recycling scrap and using eco sustainable material. Through focusing upon sustainability, the businesses reduce their carbon footprint, but improving their sustainability in a market that is becoming more eco-conscious.
In the end, die casting has been a key component of the manufacturing industry in Malaysia that has boosted innovation and improved effectiveness in a variety of key industries. Die casting’s accuracy, precision, adaptability, and efficacy make it an essential part of sectors like aerospace, automotive, and electronic components. In the meantime, as Malaysia remains focused on maintaining its high standards of production the process of die casting continues to be an important tool to satisfy market demands from around the globe. In the ongoing effort to invest in environmentally sustainable practices as well as cutting-edge technology ensures that die casting is a reality in Malaysia remains environmentally friendly, competitive and ready to serve the ever-changing needs of domestic and international industry. Due to its capability of producing quality, affordable parts in a short time and efficiently and efficiently, die casting will continue to play an important part in shaping how manufacturing will develop in Malaysia.